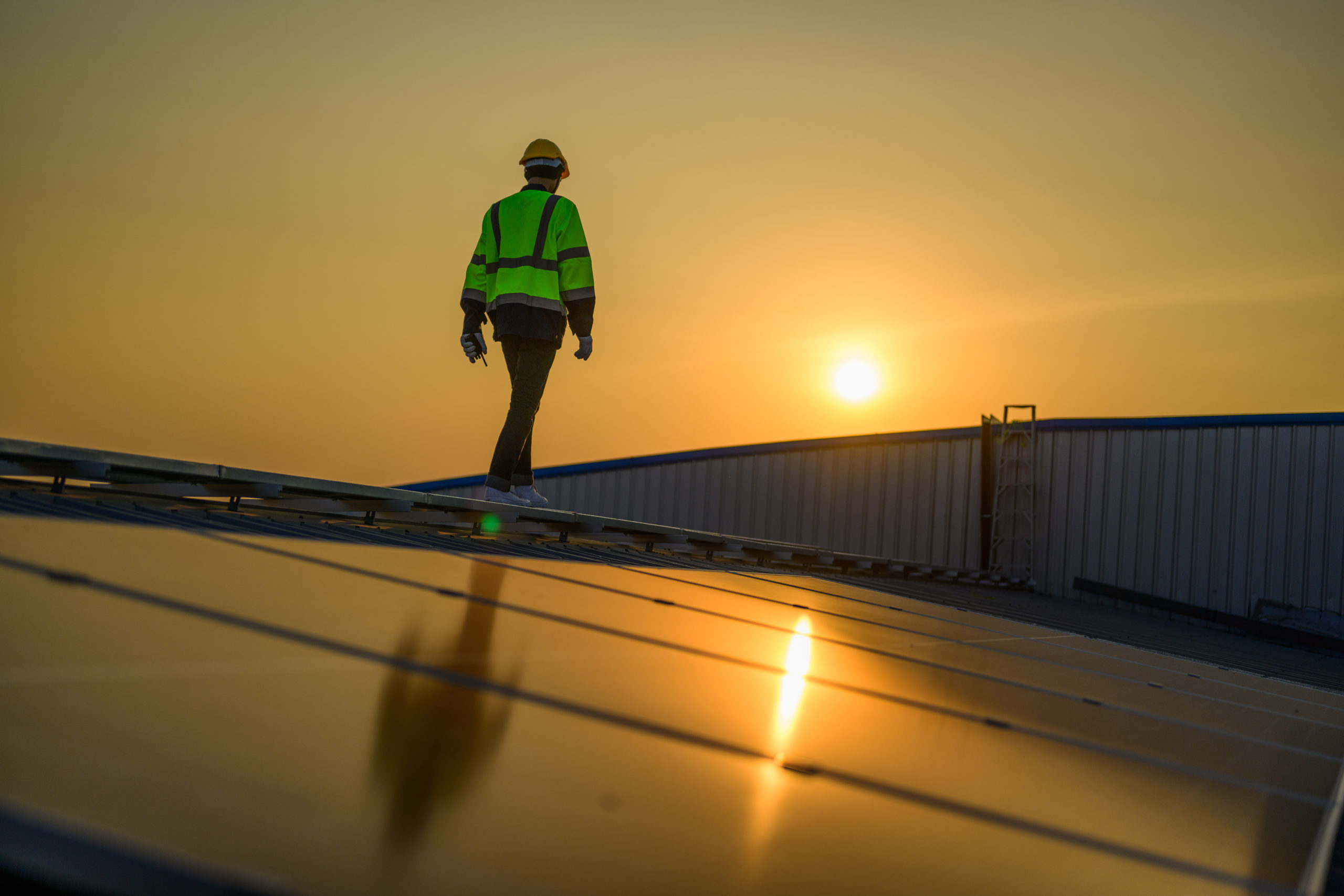
18 March 2024
Sustainability in Manufacturing: A Comprehensive Guide
In recent years, the manufacturing sector has taken significant strides towards eco-friendly practices. Sustainability in manufacturing entails a strategic approach to producing goods economically whilst minimising waste and reducing negative environmental impacts, but in the quest for carbon neutrality, the UK still has a considerable journey ahead. The attainment of net zero by 2050 hinges greatly on government collaboration with businesses across the country who intend to adapt to the current climate crisis.
This guide aims to explore the essence of sustainable manufacturing: its elements, challenges, best practices and examples - for all businesses seeking to embrace eco-conscious practices.
What is sustainable manufacturing?
Sustainable manufacturing involves the strategic creation of products through efficient means and use of components that minimise waste and mitigate environmental harm. With mounting pressure on businesses to curb carbon emissions, sustainable manufacturing has emerged as a pivotal strategy for reducing environmental footprint and fostering long-term viability.The rise of sustainability in manufacturing
The impetus for sustainability in manufacturing has gained momentum in recent years, with a growing number of companies recognising its significance in both responding to the climate crisis and bolstering growth and global competitiveness. According to KPMG's Survey of Sustainability Reporting in 2020, 80 percent of the world's leading companies are integrating sustainability into their operations and objectives. Additionally, consumer preferences are shifting towards environmentally friendly products, with more than a third of global consumers willing to pay a premium for sustainable goods. This paradigm shift underscores the imperative for manufacturers to adopt sustainable practices to meet evolving market demands.Examples
A snapshot of three companies leading the way in the UK are Taylors of Harrogate (the Bettys brand and Yorkshire Tea), Siemens and Quorn. Taylors of Harrogate aims for sustainable plastic packaging by 2025, achieving carbon neutrality through carbon offsetting since 2015, including tree planting initiatives. Siemens, the UK manufacturing giant, recycles 92% of materials, spearheading projects like the Keele University Smart Energy Network Demonstrator, reducing 4,000 tonnes of CO2 yearly. Committed to renewable energy, Siemens' blade factory in Hull, with £160m UK government investment, powers 1.3 million homes through projects like Hornsea Two. Quorn, based in Yorkshire, focuses on recycled packaging and minimising plastic usage, with its meat-free alternatives touted to reduce greenhouse gases significantly.Challenges in achieving sustainable manufacturing
Assessing the sustainability of a manufacturing system entails examining various aspects, including manufacturing costs, power consumption, waste management strategies, operational safety measures, personnel health safeguards and environmental friendliness initiatives. Despite the growing recognition of sustainability's importance, several challenges impede its widespread adoption:Cost constraints
Initial high costs and longer payback periods deter businesses from investing in sustainability.Lack of standardised metrics
Inadequate systems for monitoring and evaluating sustainability initiatives.A consumer awareness gap
Despite demand for green products, consumer awareness of sustainable practices remains limited.Limited awareness and innovation
Insufficient access to sustainability-oriented research and programmes hampers innovation.Best Practices in Sustainable Manufacturing
To navigate these challenges and foster sustainable manufacturing, companies can adopt the following best practices to mitigate their environmental impact:1. Energy efficiency
Incorporating renewable energy sources such as solar or wind power into manufacturing operations can significantly reduce reliance on fossil fuels. While the initial investment may be substantial, the long-term benefits include cost savings on energy expenses and a substantial decrease in carbon emissions. By transitioning to renewable energy, and optimising energy consumption, manufacturers not only contribute to environmental preservation but also futureproof their businesses against volatile energy prices.2. Upgrade of facility and production processes
Upgrading factory infrastructure and production processes with sustainability in mind can yield dual benefits. Improved operational efficiency not only enhances profitability but also serves as a compelling selling point for attracting new clients. By investing in sustainable upgrades, manufacturers demonstrate their commitment to continuing eco-conscious practices.3. Waste and pollution reduction
Implementing strategies to minimise waste generation and promote recycling is essential for curbing pollution in manufacturing. Strategies such as lean manufacturing, just-in-time production and material substitution enable businesses to streamline operations, minimise waste generation and mitigate pollution at its source. Robust recycling programmes and exploring innovative ‘clean’ technologies for recovering valuable materials from waste streams means manufacturers can minimise landfill waste and conserve finite resources. Technologies such as catalytic converters, electrostatic precipitators and scrubbers help capture and neutralise pollutants before they are released into the atmosphere, safeguarding air quality and minimising environmental harm.4. Use of sustainable materials
Seeking alternatives for materials that are environmentally harmful or resource-intensive and embracing circular economy principles can help companies in the march to net zero. A circular economy is an economic model that keeps products and materials in use for as long as possible and is paramount to reducing waste and promoting sustainability. By prioritising the sourcing of eco-friendly and recycled materials, businesses can minimise their environmental footprint with the four key steps of a circular economy: sourcing, manufacture, use and recovery. Manufacturers play a pivotal role in mitigating environmental impact through sustainable practices. By prioritising energy efficiency, waste reduction and the use of sustainable materials, businesses can lower their carbon emissions while ensuring long-term viability and competitiveness. Even incremental changes in existing processes can yield substantial benefits and, by embracing eco-friendly practices, manufacturers not only fulfil their environmental responsibilities but can also position themselves as leaders in a rapidly evolving marketplace.Read more blogs from Ascend:
Addressing the skills gap in the Engineering Industry Manufacturing recruitment challenges in 2024Need further advice? Our expert team at Ascend are knowledgeable on all aspects of the engineering industry and the challenges of its insurance needs.
Contact Chris Buchholz today on 07842 021430 or by email, Chris.Buchholz@ascendbroking.co.uk.

Recent Posts
Ascend Broking
ASCEND BROKING GROUP LAUNCHES ASCEND RISK
Ascend Broking