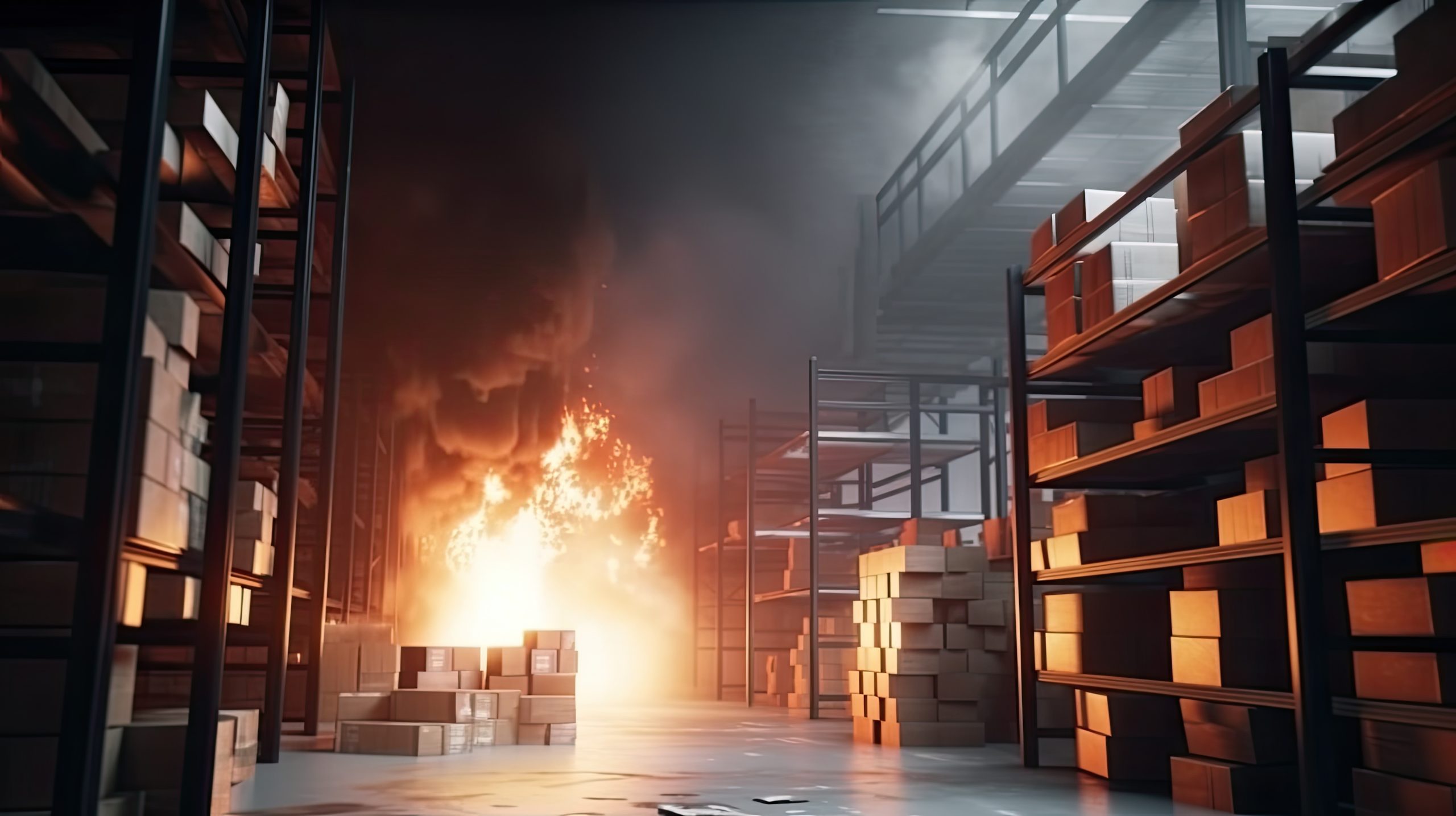
11 January 2024
Managing Fire Risks in the Manufacturing Industry
Fire safety is of paramount importance to all businesses. But in the dynamic landscape of the manufacturing industry there’s a particularly high risk.
The manufacturing sector is particularly vulnerable to fire hazards due to the presence of flammable materials, complex machinery and high-energy processes in its factories - and the amount of stock in its warehouses. This blog explores the industry’s key risks and highlights the proactive measures and best practices for managing fire risks and ensuring a secure working environment.
Key fire risks
- Storerooms and warehouses with storage of large quantities of flammable goods under limited supervision - for example, wood, paper and textiles.
- Machinery that experiences some kind of malfunction. A significant number result from inadequate maintenance, operator error or unauthorised repairs.
- Electrical apparatus, wiring, systems and lighting malfunctioning due to misuse or faults from irregular servicing.
- Carelessly discarded smoking materials, especially when coming into contact with flammable items.
- Kitchenettes or tea rooms, depending on the equipment used - especially if unattended cooking, or oils and fats are involved.
- The misuse of flammable liquids and gases.
- Heating equipment failure or malfunction.
- Tradespeople on the premises, especially if they use blow lamps or power tools that create sparks.
- Oil spillages or toxic fluid spillages.
- Vehicle and forklift malfunctions or misuse.
Fire risk management
Fire Risk Assessments are a requirement by law, as part of the Regulatory Reform (Fire Safety) Order of 2005, which applies to England and Wales. A comprehensive Fire Risk Assessment will identify potential ignition sources, flammable materials and vulnerable areas. The layout of the facility will be assessed, as well as the nature of all manufacturing processes and the presence of any electrical or mechanical equipment that could pose a fire risk. This initial step lays the foundation for developing a targeted and effective fire safety plan. Following a Fire Risk Assessment, a business may find they can introduce a simple measure like dividing their stock into two - and between two separated warehouses - so if a fire occurs, 50% of stock would remain, and the business can carry on trading. Another example would be to create duplicate copies of business records and store them in a separate building from your offices. Make sure consequential fire losses are taken into consideration in any risk assessments, as these sometimes result in a company facing bankruptcy after a fire. When it comes to visiting tradespeople, enforce rigorous supervision and make suitable firefighting equipment available during and after their work. Conduct thorough inspections of the areas they have worked in to identify and address any overlooked hot spots or small fires.Fire-resistant design and construction
When constructing or renovating manufacturing facilities, prioritise fire-resistant materials and design elements. Fire-resistant walls, ceilings and floors can contain the spread of fire, limiting its impact on the overall facility. Additionally, invest in fire-rated doors and windows to create compartmentalised zones, preventing the rapid escalation of flames.Fire suppression systems
Deploying advanced fire suppression systems is crucial for swift and effective response in the event of a fire. Automatic sprinkler systems, fire extinguishers and fire blankets should be strategically placed throughout factories, warehouses and kitchens. Regular maintenance and testing of these systems are essential to ensure their functionality when needed.Regular equipment maintenance
Malfunctioning machinery or electrical systems can be a significant contributor to fire risks in manufacturing facilities. Establish a routine maintenance and cleaning schedule for all equipment and conduct regular inspections to identify and address potential issues promptly. Replace or repair any faulty components to reduce the likelihood of equipment-related fires.Monitoring and control of combustible dust
Certain manufacturing processes generate combustible dust, which can pose a severe fire hazard. Implement effective dust collection and ventilation systems to control the accumulation of combustible dust. Regularly clean and maintain these systems to prevent the risk of ignition.Staff training
Employee awareness and preparedness play a pivotal role in preventing and mitigating fire risks. Staff fire training sessions – required by law - should not only take into account what to do if a fire breaks out. They should also focus on simple fire precautions to prevent fires happening in the first place. Comprehensive training sessions should be conducted to educate employees about fire hazards, safe work practices and the proper use of fire safety equipment. A culture of vigilance and responsibility is best encouraged, empowering every team member to play a role in fire prevention and response.Emergency response protocols
A comprehensive evacuation plan reduces risks and protects against all types of fire hazards. Developing and regularly practicing emergency response protocols is fundamental to managing fire risks. Conduct fire drills to familiarise employees with evacuation routes, assembly points and proper use of firefighting equipment. Designate and train specific personnel to act as fire wardens, responsible for guiding others to safety during an emergency. Install fire safety signage across the premises to provide clear guidance during emergencies, plus fire extinguisher identification signs, visible on each fire extinguisher, indicating the extinguisher type and the classes of fire it is suitable for. Additionally, fire exit, fire door and assembly point signs should be prominently displayed throughout buildings.Arson prevention
Arson is, sadly, a predominant factor behind fires in business premises, constituting 45% of all significant fire incidents. Most of these incidents are not purposefully planned, with the majority being spontaneous acts of vandalism, but a manufacturing business holds a duty to minimise this risk. In the fast-paced world of manufacturing, managing fire risks is a critical aspect of ensuring both the safety of personnel and the continuity of operations. A comprehensive approach, combining risk assessment, preventive measures, employee training and emergency response planning can significantly reduce the likelihood and impact of fires in manufacturing facilities. By prioritising fire safety, manufacturers can create a secure working environment that fosters productivity and success.Other Blogs that may be of interest:
Fire in Industrial or Manufacturing Properties | NFPA Research Why insurers refuse claims from your company Warehouse conditions (ascendbroking.co.uk) Why all businesses require Directors and Officers insurance (ascendbroking.co.uk)Any questions? Please don’t hesitate to contact one of our team.
Chris.buchholz@ascendbroking.co.uk| Mobile: 07842 021430
Recent Posts
Ascend Broking
ASCEND BROKING GROUP LAUNCHES ASCEND RISK
Ascend Broking